Штампование
Штампование, механический процесс получения изделий требуемой формы из металлов и других пластических материалов посредством выдавливания в металлические изложницы, «штампы», имеющие соответствующие изделию контуры или рельеф. Таким образом, возможно изготовлять большое число изделий (штамповок), совершенно одинаковых по форме и размерам. Штампование основано на пластическом состоянии материалов, которые под давлением текут, заполняя пустоты в штампах. Массивные толстые штамповки получаются посредством горячего штампования, когда металл, нагретый до определенной температуры (т. н. ковочного жара), приходит в вязкое тестообразное состояние и под давлением, производимым кувалдами или машинами (молотами, прессами, см. XX, прил. железоделательное производство, 55 сл.), заполняет металлические формы — «штампы», откуда получается в виде готового изделия, соответствующего как бы отпечатку формы штампа (фиг. 1 — 4). В случае более сложных форм изделий, последние проходят ряд последовательных переходов в штампах, видоизменяющих свой рельеф и контуры. Тонкие и небольшие изделия получаются посредством холодного штампования, когда текучесть вязкого металла и т. п. в тонких слоях достаточно велика и допускает пластическое изменение форм до известных пределов, после чего, при глубоких и сложных формах рельефа штампов, материал переходит предел упругости, становится слишком жестким и рвется, почему приходится восстанавливать вязкость путем отжига для дальнейших переходов штамповка.
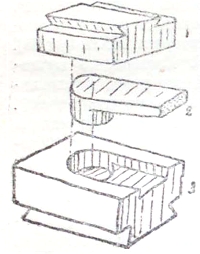
Фиг. 1. Штамп односторонний (из одной части, открытый) для бобышки рычага. 1 – верхний плоский боек молота или пресса; 2 – изделие; 3 – штамп (одна нижняя часть в наковальне).
Фиг. 2. Штамп двухсторонний (из двух половинок, закрытый) для бобышки рычага. 1 – верхняя часть штампа (боек пресса); 2 – направляющий (центрирующий) штифт; 3 – изделие; 4 – нижняя часть штампа (наковальня, стол пресса).
Штампование распадается на ряд различных операций, по которым изменяются формы штампов и род машин. Вырезные (прорезные, пробивные фиг. 5—6) штампы производят разрезку, пробивку и вырезку определенных форм из листов и полос. Вытяжные штампы (фиг. 8) производят вытяжку из листов глубоких форм и углублений разного контура (гильз, труб и т. п.). Загибочные штампы производят загибку разных участков металла на требуемую форму (фиг. 9 и 10). Сложные штампы производят последовательно или одновременно вырезку, пробивку, загибку, вытяжку и пр.
Фиг. 3 а — ручной штамп открытый (гвоздильня для головок болтов): б — ручной штамп, закрытый для обжима буртика или обварка (утолщенного кольца на валу).
Фиг. 4. Штамп из двух половинок (симметричных) для головки шатуна. 1 – боек; 2 – верхняя часть штампа; 3 – нижняя часть штампа; 4 – наковальня; 5 – изделие.
Фиг. 5. Вырезной штамп (для пробивки дыр и высечки). 1 – верхняя часть штампа; 2 – пуансоны-пробойники; 3 – пуансон просечной; 4 – изделие; 5 – высечка (отход металла); 6 – нижняя часть штампа; 7 – матрица.
Фиг. 6. Вырезной (просечной) штамп. 1 – пуансон; 2- высечка, облой (отход металла); 3 – изделие; 4 –матрица.
Фиг. 7. Пробивной штамп. 1- верхняя часть штампа (боек); 2 – пуансон; 3 – съемник; 4 – матрица; 5 – нижняя часть штампа (наковальня, стол).
Фиг. 8. Вытяжной штамп. 1 – верхняя часть штампа; 2 – зажим; 3 – пуансон; 4 – матрица; 5 – нижняя часть штампа; 6 – изделие.
Фиг. 9. Загибочный штамп для полосы. 1 – верхняя часть; 2 – изделие; 3 – нижняя часть.
Фиг. 10. Загибочный штамп для коленчатого вала. 1 – верхняя часть, 2 – изделие, 3 – нижняя часть.
Фиг. 11. Клепка машинная (налево) и ручная (направо). 1 – поддержка; 2 – склепанные листы; 3 – прижим листов; 4 – обжимка (штамп); 5 – наконечник клеп-машины; 6 – молот.
Фиг. 12. Чеканка европейская (а) и американская (б).
Штампование применяется для массового производства мелких предметов: различных деталей пишущих, счетных, швейных, текстильных, сельскохозяйственных и других машин, оружия, велосипедов, автомобилей, самолетов и пр. В этом случае предметы производятся в большом числе прямо из сортового материала, без предварительной обработки, посредством штампов надлежащей формы, изготовленных на высококачественной твердой стали, причем иногда изделие, для получения сложной формы, проходит последовательно несколько штампов. Для производства небольшого числа сравнительно крупных деталей машин изделие подготовляется ковкой ручным способом или в более простых штампах и такая заготовка поступает в окончательный штамп для придания ей надлежащей формы, почему штамп изготовляется из чугуна или других материалов, менее прочных и более дешевых.
Изготовление штампов представляет очень сложную операцию и требует большой квалификации, опытности и затраты времени и средств. Поэтому сложный штамп окупается только производством большого числа одинаковых изделий зато они выходят очень точных размеров, иногда не требуют никакой дополнительной обработки. Для изготовления штампов составляются особые чертежи, по коим изготовляются шаблоны из листового железа, служащие для отковки и точной механической обработки частей штампов, подвергающихся весьма тщательной ручной слесарной пригонке и термической обработке (закалке). Штампы могут состоять из одной части (открытые штампы), или из двух частей (закрытые штампы), или из нескольких совместно работающих частей (сложные штампы). Штампы из одной части применяются для изготовления деталей очень простых форм (например, для штамповки головки болта, заклепки и т. п.). Обычно штампы состоят из двух частей с соответствующим рельефом и контуром в обеих частях, образующих углубление, в которое и затекает штампуемый материал, причем обе половины штампа должны быть изготовлены таким образом, чтобы изделие легко вынималось из них при разъеме штампов.
Для проверки точности штампов обычно собранные вместе половинки заливаются расплавленным свинцом и отпечаток его контролирует правильность формы штампов. Штампы закрепляются в штамповочных машинах (прессах и молотах) клиньями, для чего делаются в закрепляющейся части штампов вырезы в виде ласточкина хвоста, входящие в соответствующие части падающей части молота и его наковальни. Срок службы штампов весьма различен в зависимости от размеров, формы и материала штамповки, а также материала и закалки самого штампа; по тому один штамп может выдержать от нескольких сотен до нескольких сотен тысяч штамповок. Одна часть штампа, обычно верхняя у прорезных и вытяжных штампов, называется пуансоном (см. пунсон), а соответствующая ей нижняя часть – матрицей. Зазоры между пуансоном и матрицей делаются очень малыми и требуют особо тщательно пригонки и отделки заточкой на шлифовальных точильных станках. Для горячей штамповки (в горячем состоянии) применяются паровые, пневматические молоты, фрикционные падающие и винтовые приводные прессы, гидравлические прессы, ковочные машины (ваксы, бульдозеры, см. XXVI, приложение кузнечное дело, 6 сл.), вращающиеся вальцы, секторальные вальцы и прочие штамповочные машины. Для холодного штампования применяются приводные фрикционные винтовые и эксцентриковые прессы, гидравлические прессы и особые штамповочные станки и приспособления. Одним из видов штамповки является клепка (фиг. 11), заключающаяся в обжатии головок-заклепок (см.). т. е., кусков металла с круглой головкой, отштампованной на одном конце. Заклепка, в холодном или нагретом до ковочного жара состоянии, вставляется в дыры двух или нескольких листов металла, сложенных вместе один на другой для скрепления, и обжимается обжимкой, т. е., особым штампом с углублением, соответствующим желаемой форме головки. Клепка производится или вручную – ударами молотка по обжимке, или пневматическим молотком, приводными, пневматическими, гидравлическими клепальными машинами. Головки заклепок сжимают соединяемые листы неравномерно. Когда требуется полная герметичность шва кругом головок и на кромках (в случае котлов, баков, резервуаров), то применяется чеканка, состоящая в холодной наклепке кромок у соединенных листов и головок заклепок. Чеканка производится посредством ударов на кромки листов и заклепок особым инструментом – чеканкой, представляющим вид ручного зубила с тупым закругленным лезвием, которое не режет, а раздавливает частицы металла листа или заклепки, заставляя их плотно прилегать друг к другу. Различают чеканку европейскую и американскую. При европейской чеканке конец чеканки тупой, широкий, захватывающий около половины толщины листа, и после чеканки получается впечатление, как будто сосуд составлен из двух тонких листов, лежащих один на другом (фиг. 12а). При американской чеканке долото гораздо тоньше, с закругленным концом и выбивает в кромке листа узкую канавку (фиг. 12б). Прежде чеканка проводилась вручную, но в последние десятилетия употребляют воздушные или пневматические чеканки, или молотки, несколько похожие на врубовые машины. Сжатый воздух, приводимый к молотку, заставляет боек прыгать шесть и более тысяч раз в минуту, и работа идет очень быстро.
Чеканкой также называют выбивание узоров обычно на листовом металле при изделиях (чеканная посуда, утварь, сбруя, пояса, оружие) особыми зубилами – чеканами, ударяемыми молотками вручную, что требует особого искусства. Иногда повторяющиеся части узора выбиваются небольшими штампами – штемпелями, нанесенными на концы стальных чеканок. Таким образом, также чеканят медали, монеты из меди, серебра, золота и других металлов. Чеканка может производиться сильными приводными прессами, давящими или ударяющим на штампы одновременно с обеих сторон чеканящейся монеты.
Литература: Гофмейстер, Г. «Кузнечные штампы», 1927, Гузевич, Д., «Как изготовить кузнечный штамп», 1926; Калинин, И. и Хасин, Б., «Обработка металлов штамповкой», 1927; Кочмарек, Е., «Современное штамповальное производство», 1927; Покрандт, В., «Горячая штамповка и изготовление штампов», 1927, Селлин, В., «Глубокая штамповка», 1928; Соболев, «Фабрикация штампованных изделий»; Швейсгут, П., «Горячая штамповка», ч. 1: Методы работ и конструкция штампов, 1927; его же, «Штамповальная кузница», 1927; Гавриленко, А. П., «Механическая технология металлов», ч. II – Обработка металлов давлением (ковка, штамповка); Прегер, Э. «Обработка металлов», ч. II и III (ковка и станки); Max Kurrein, “Die Werkzeuge und Arbeitsverfahren der Pressen” 1926; Eugen Kaezmarek, “Die modern Stanzerei”, 1929; P. H. Schweissguth, “Schmieden und Pressen”, 1923; его же, «Gesenkschmied», Arbeitsweise und Konstruction der Gesenke, 1926; W. Sellin, “Die Zuchtechnik in der Blechbearbeitung”. 1926; F. A. Stanley, “Punches and Dies”, Lond.; F. H. Colvin, “Practical Die Making”, Lond.; E. Krabbe, W. Meier und W. Selin, “Stanztechnik”, ч. I, II, III, Berl., 1930; Подробная библиография по обработке металлов пластическим путем с 1835 по 1917 г. указана в американском журнале Iron Age, 1917, ноябрь, 1.
А. Бриткин.
Номер тома | 50 |
Номер (-а) страницы | 418 |